

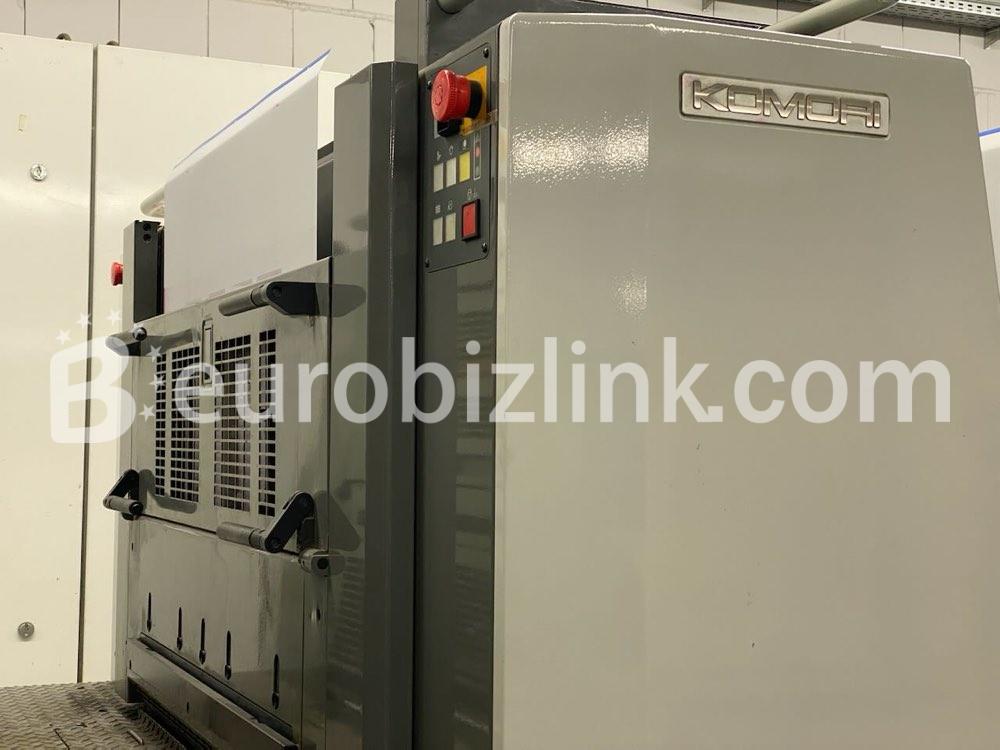
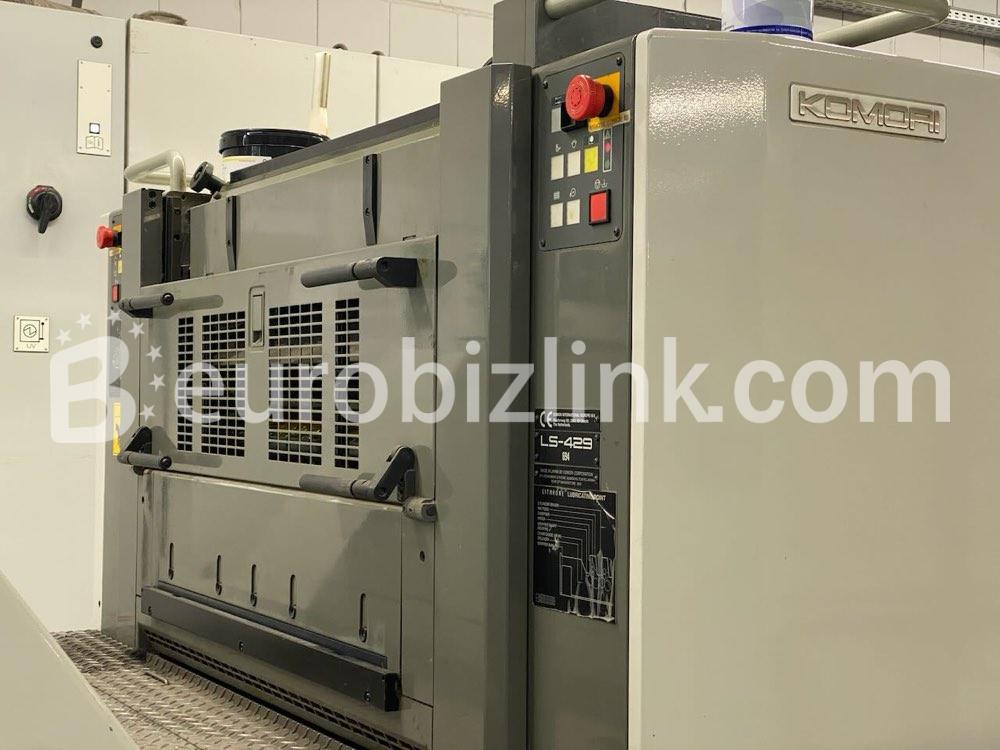
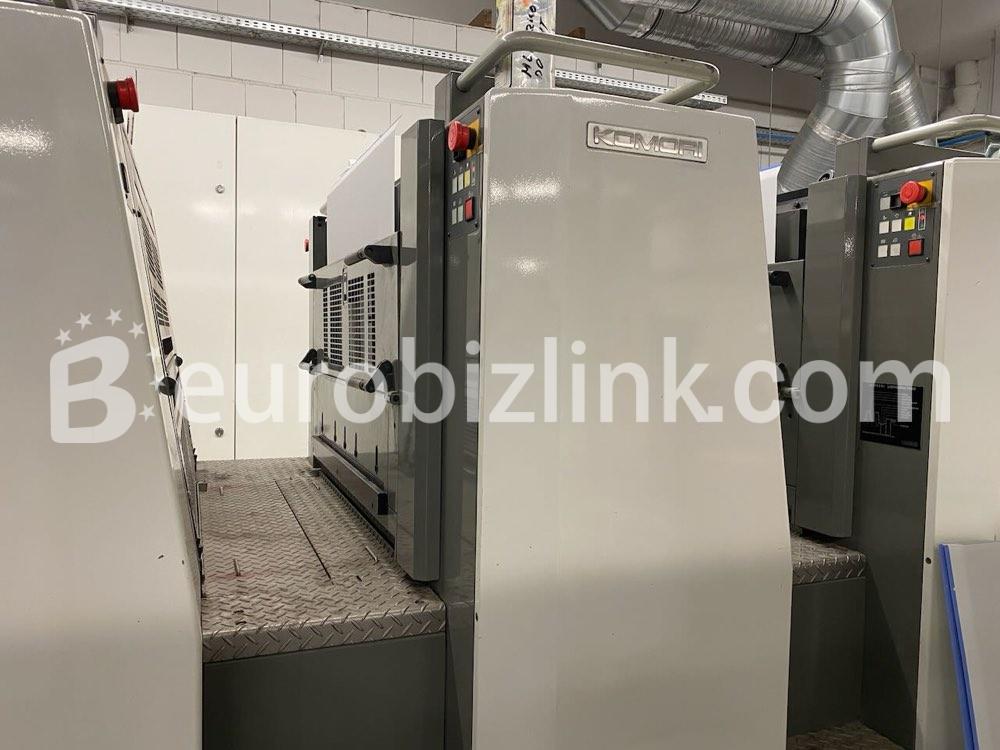
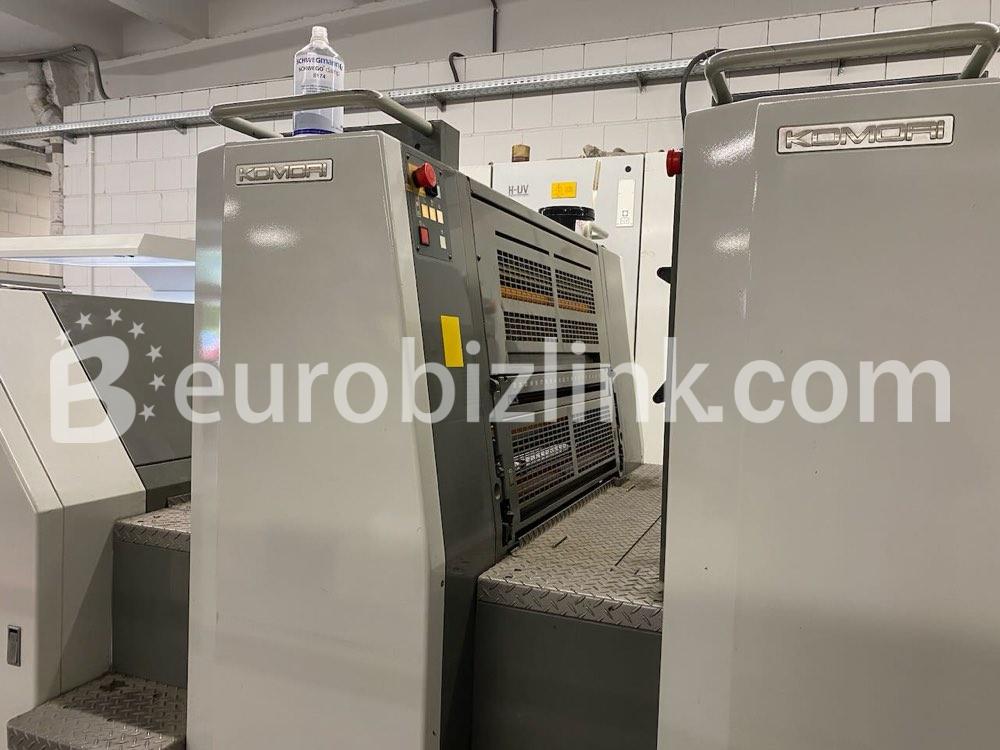
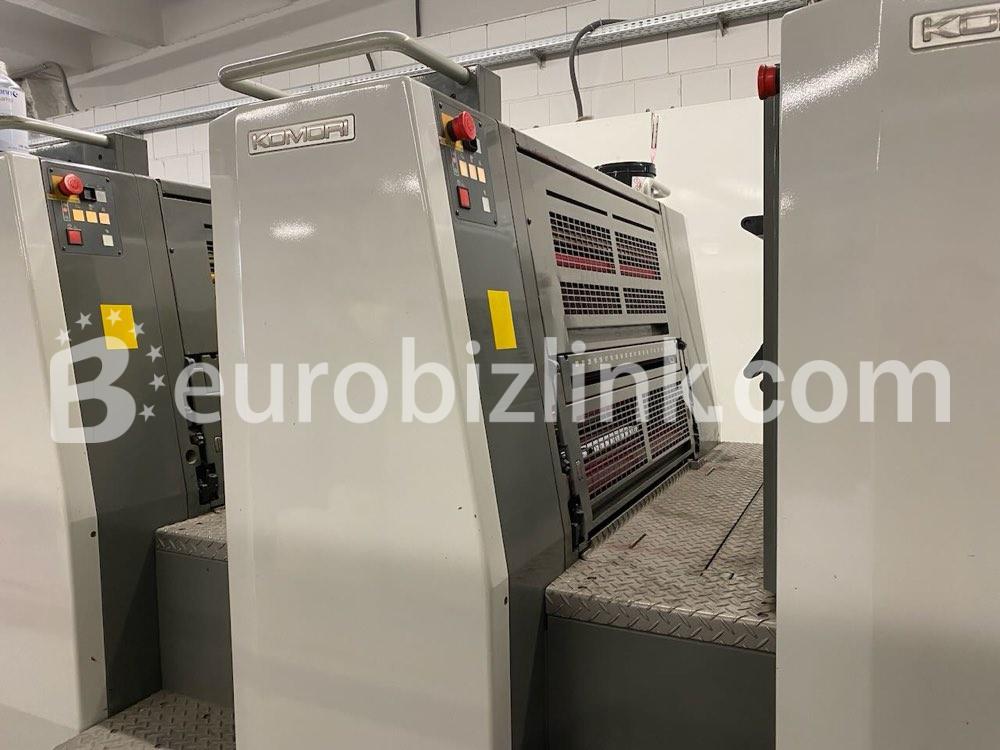
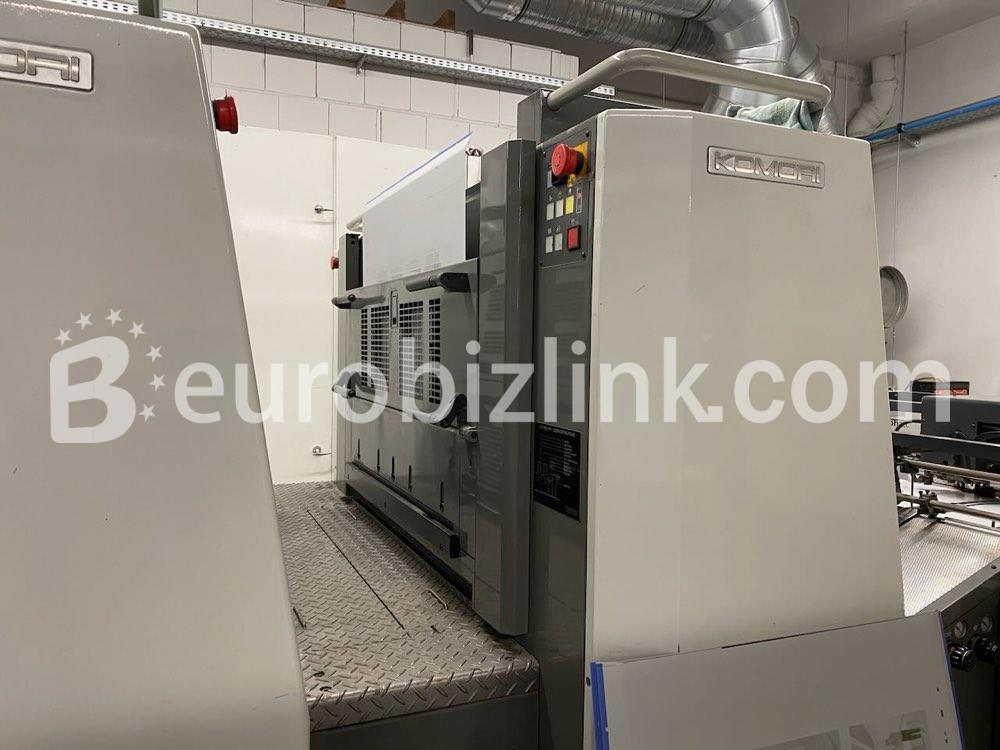
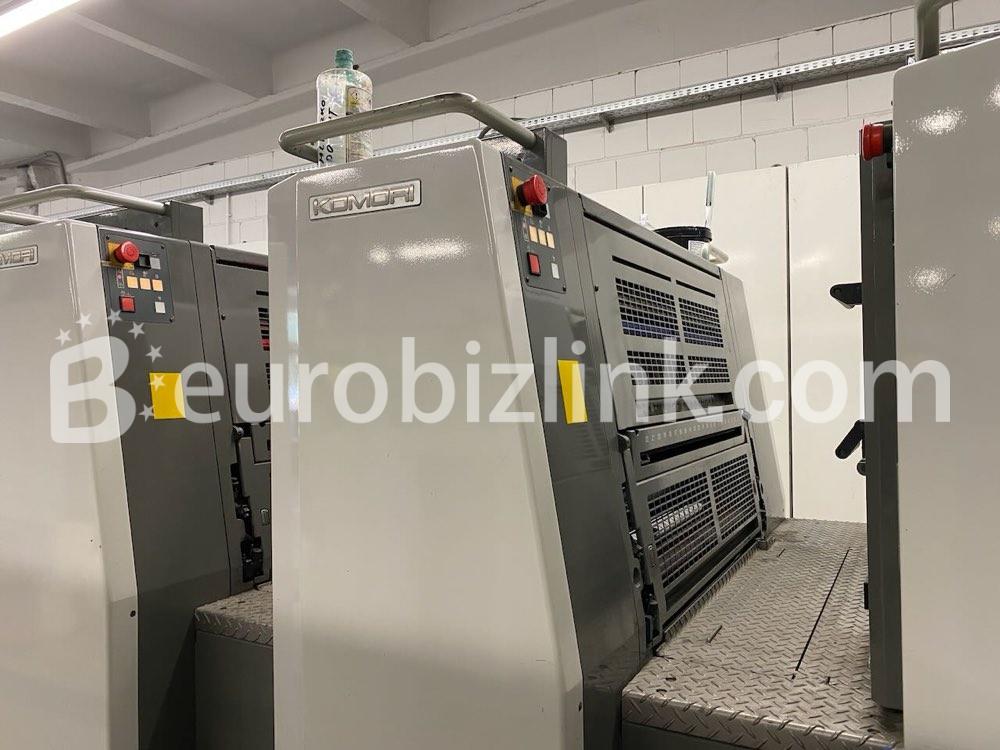
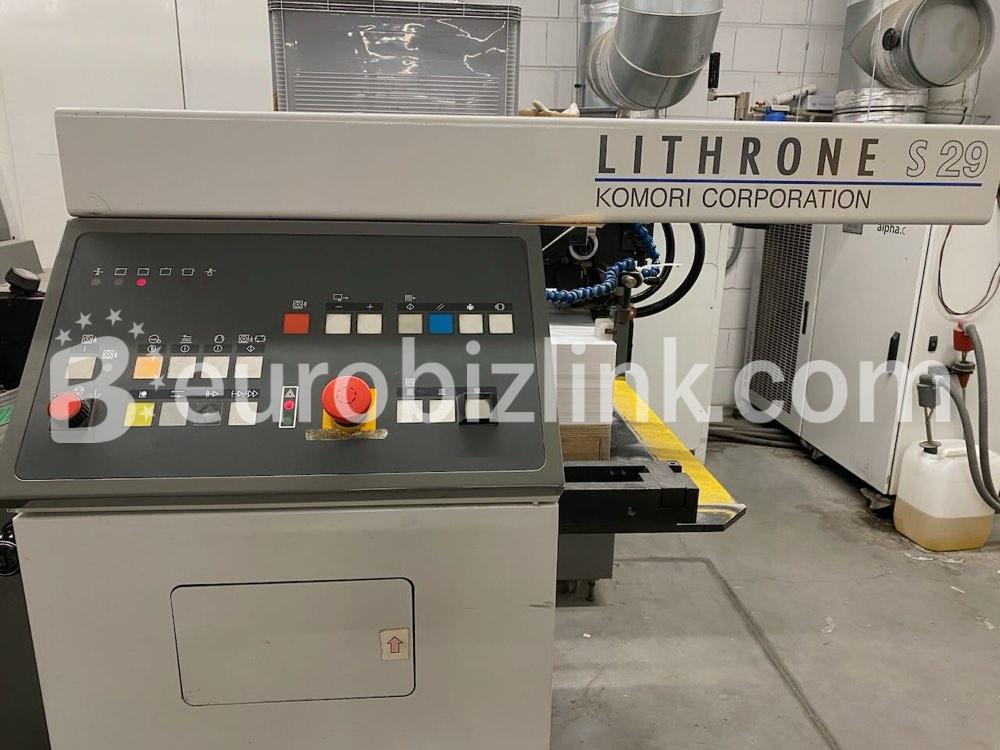
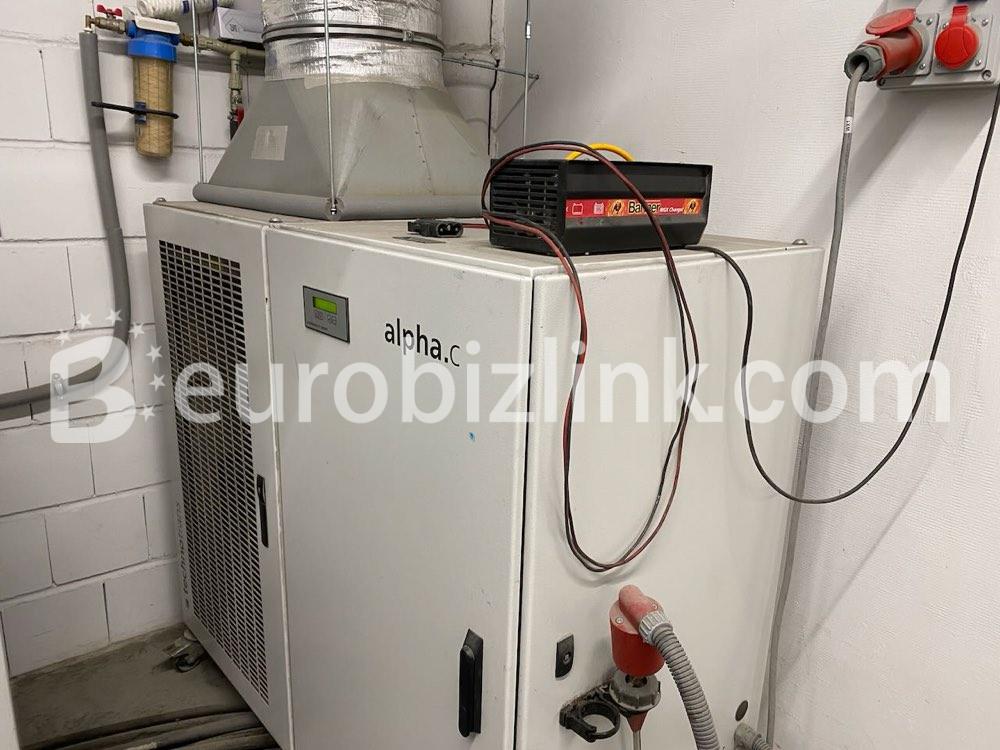
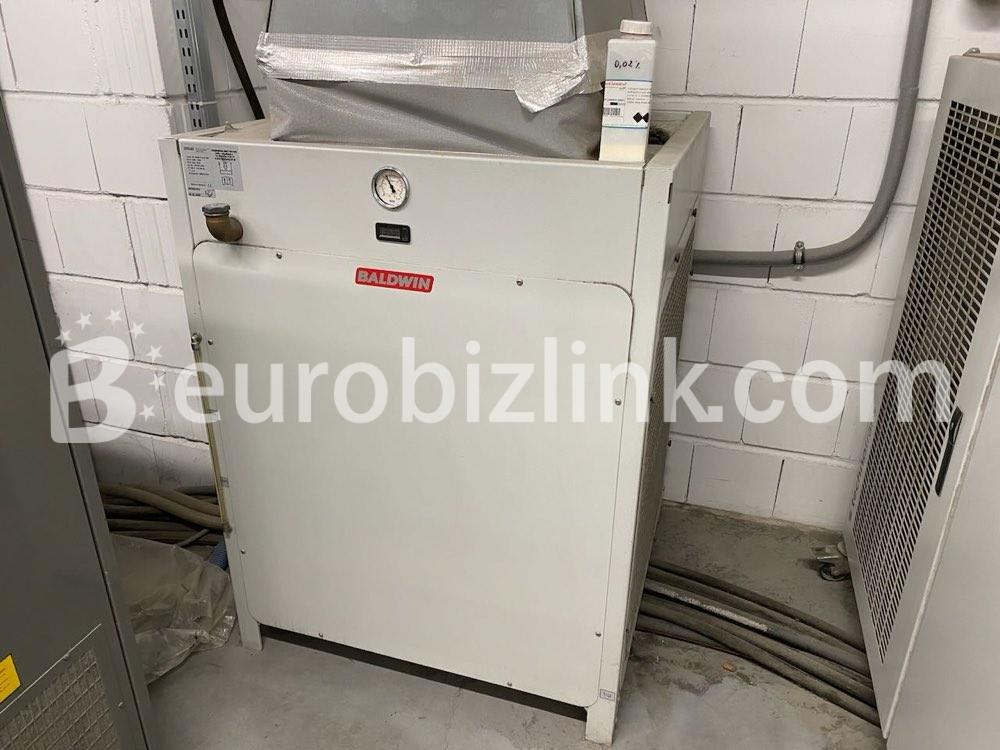
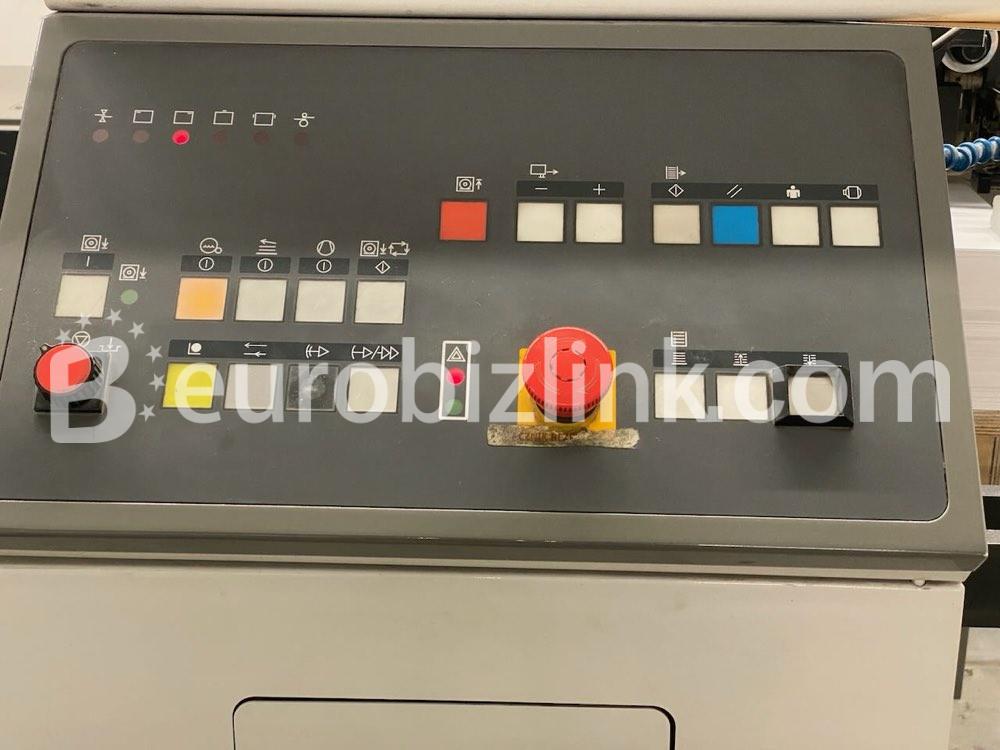
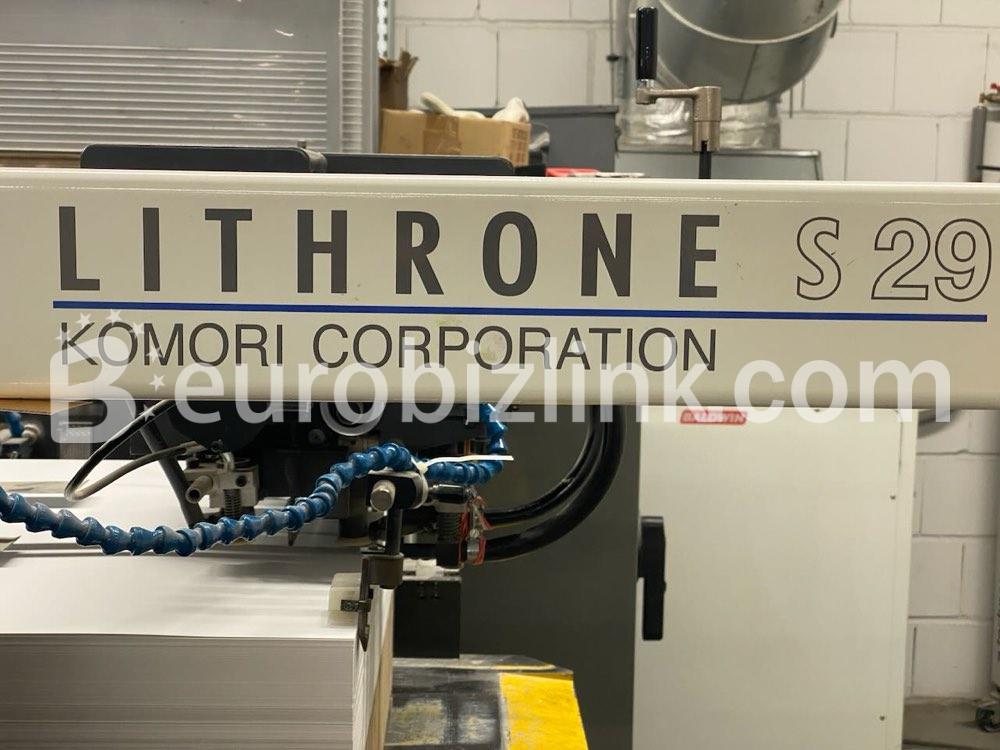
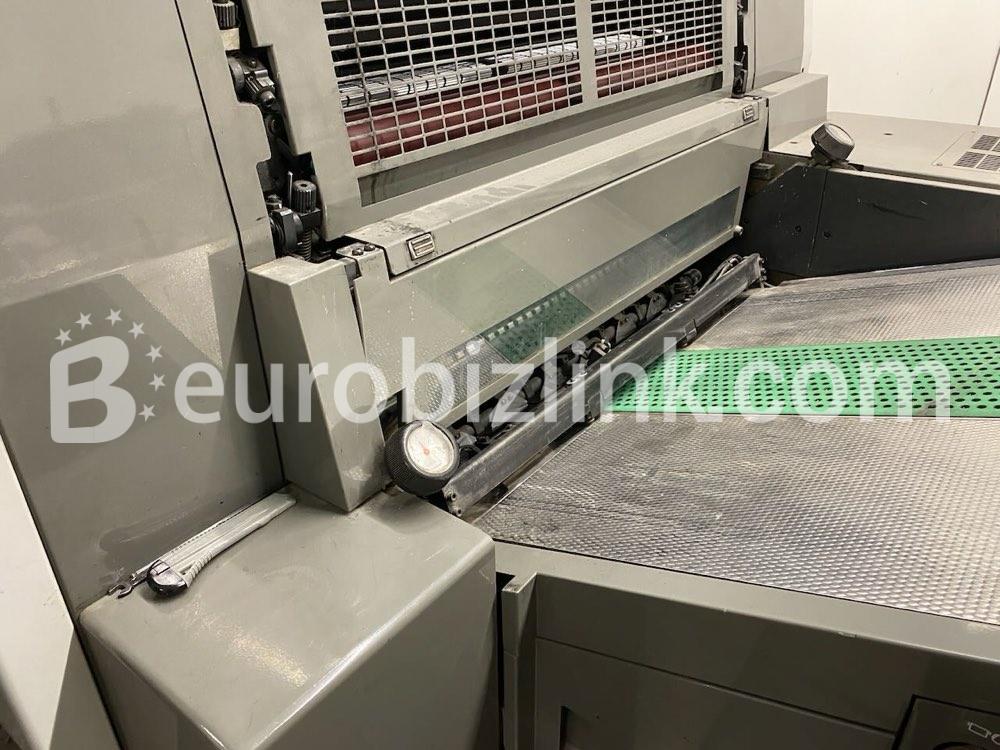
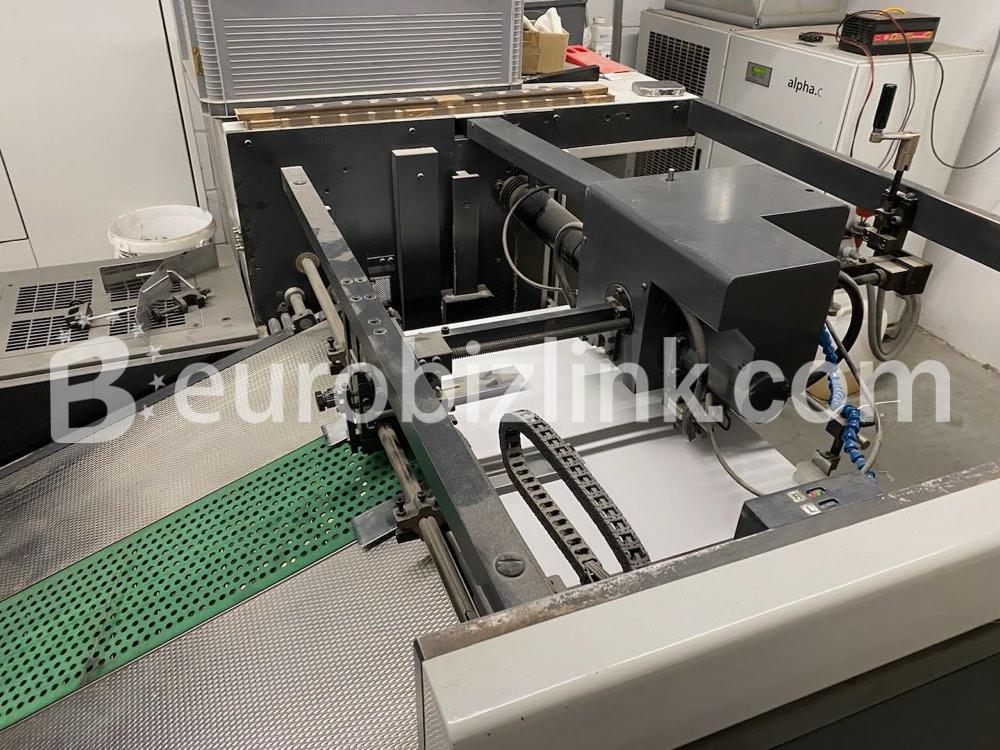
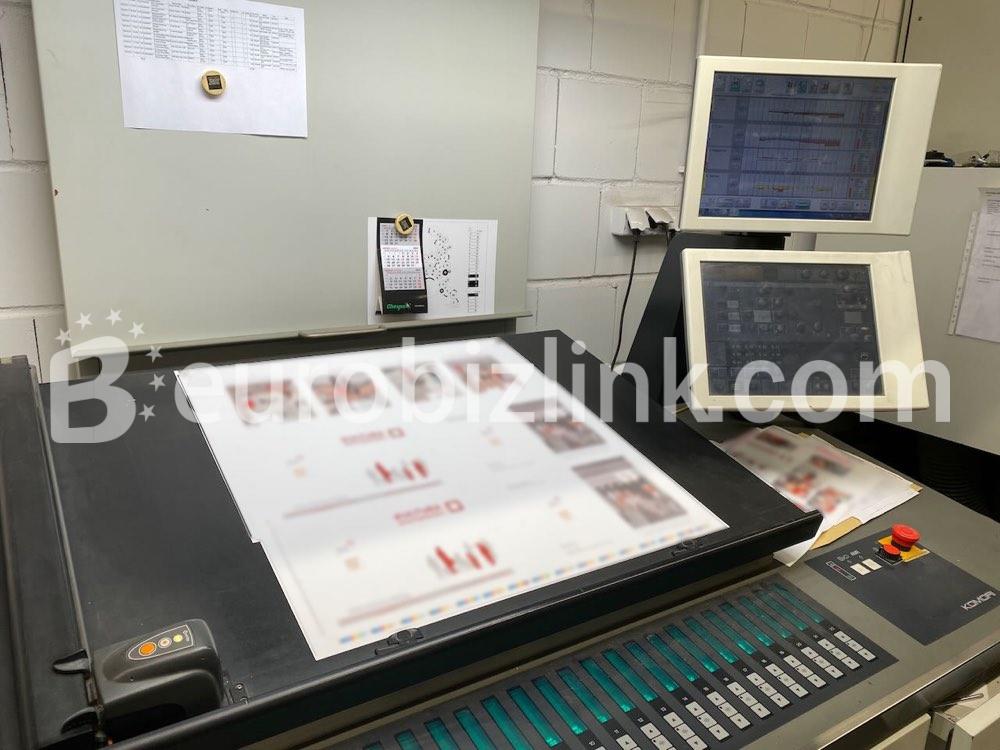
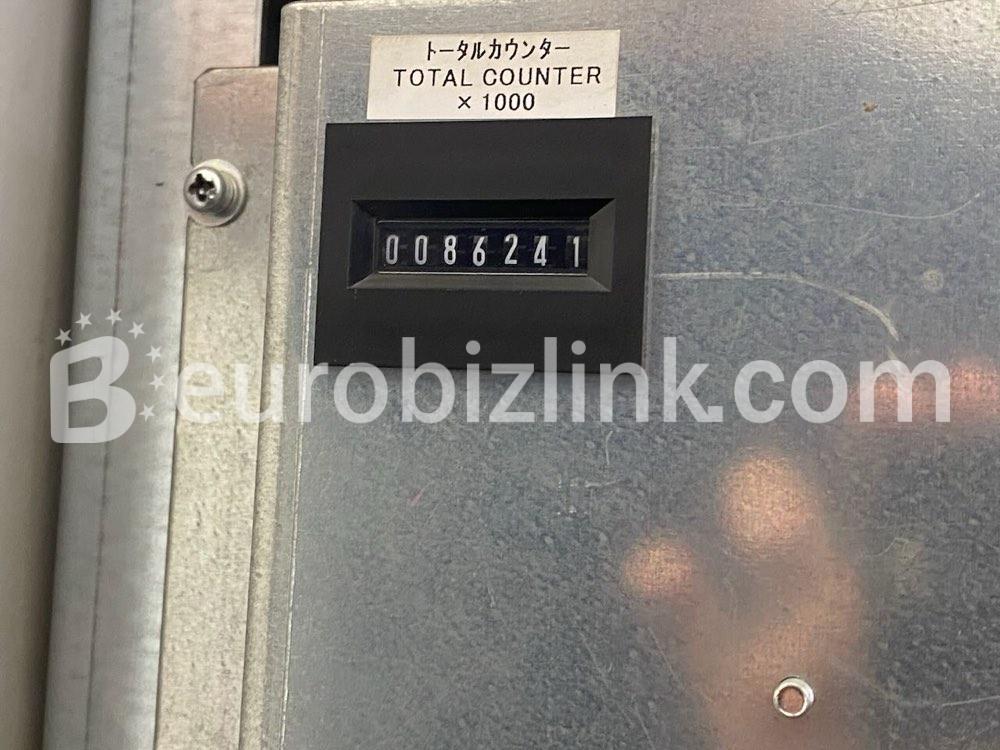
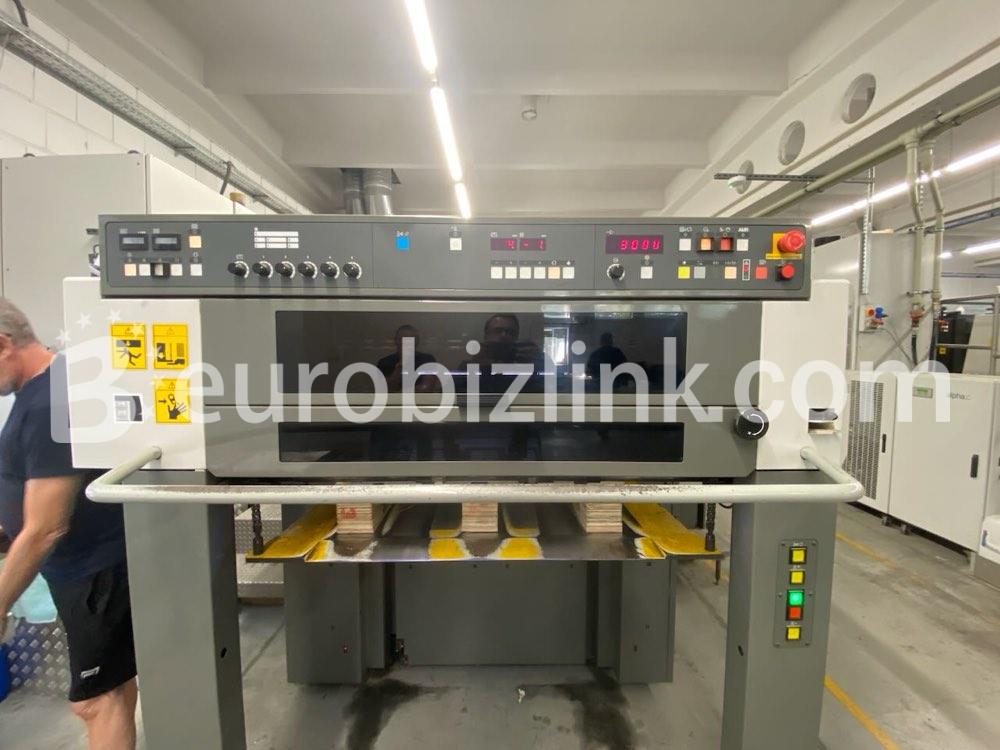
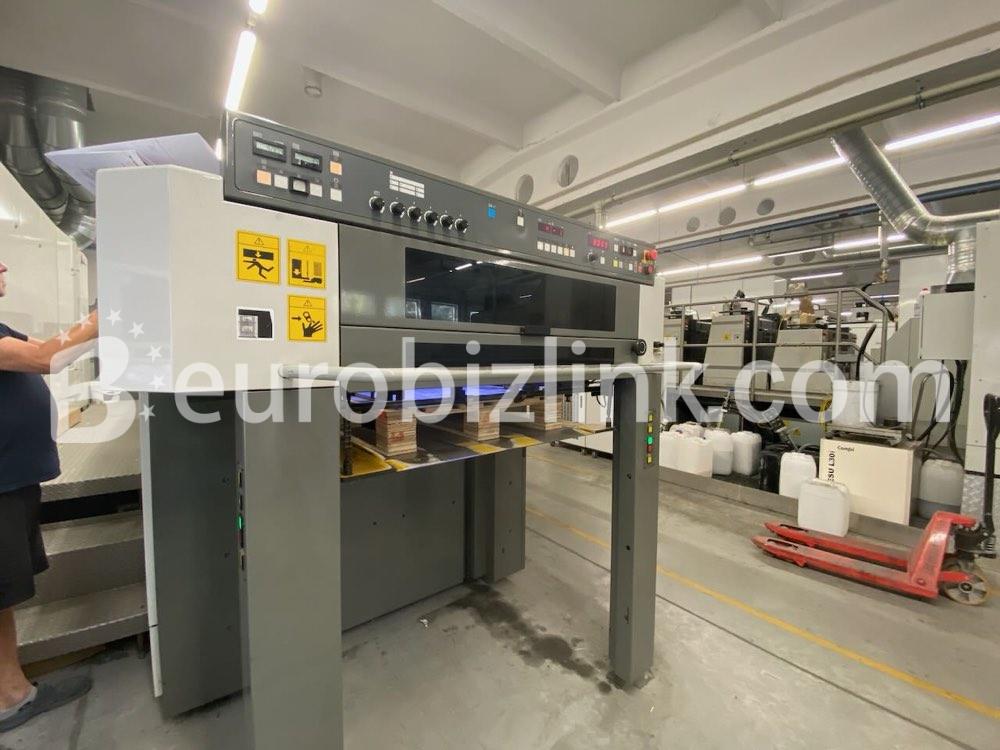
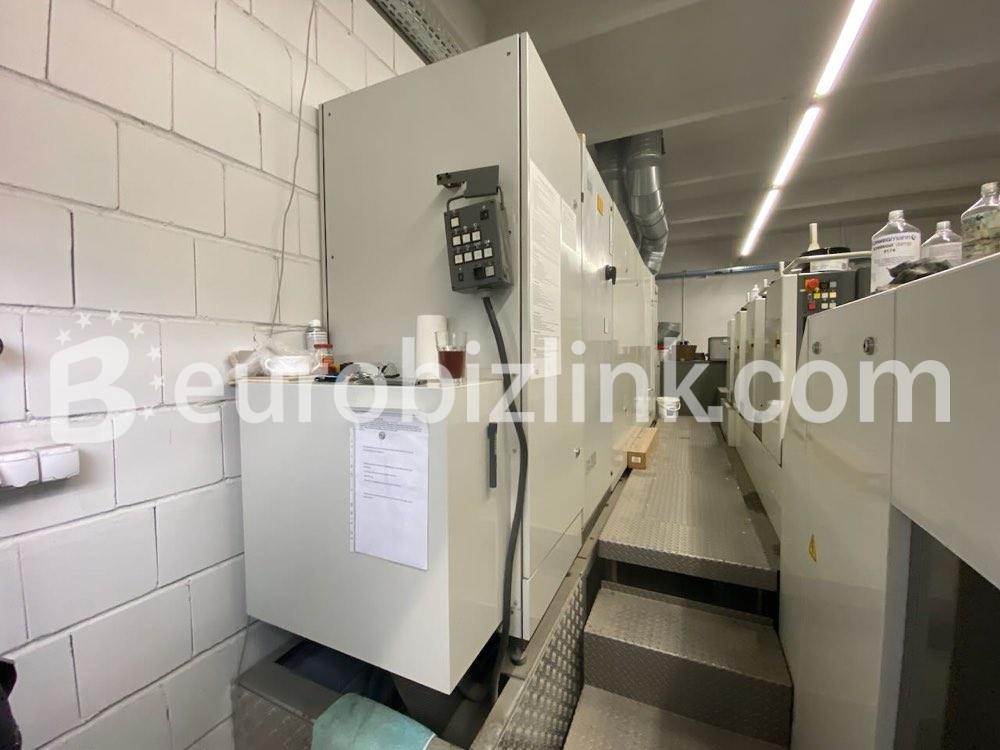
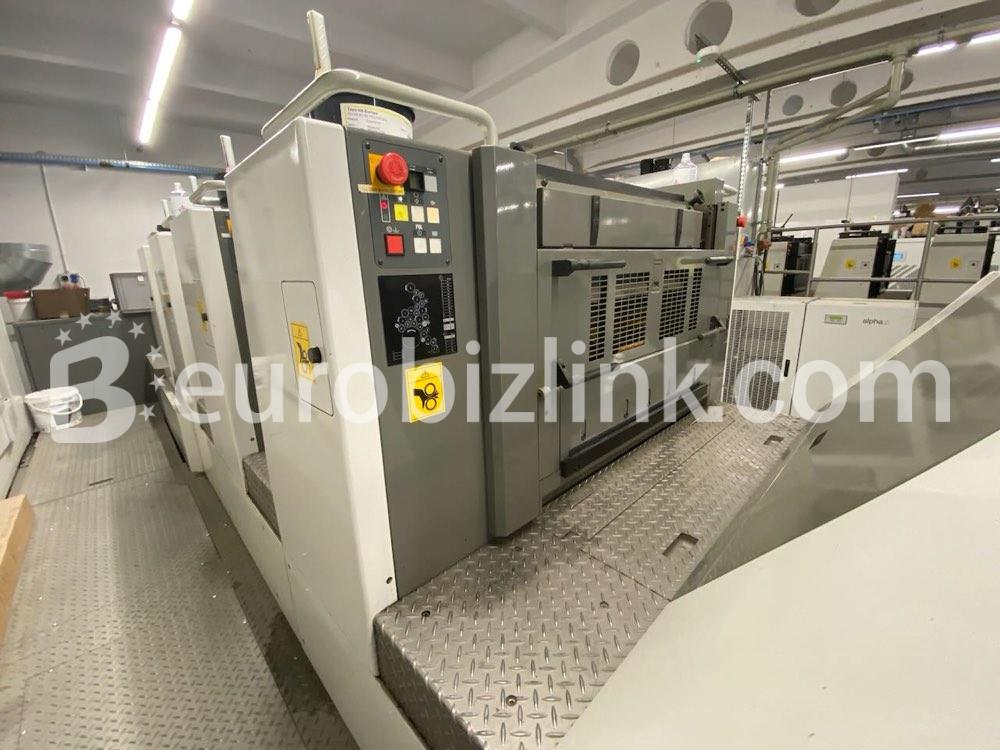
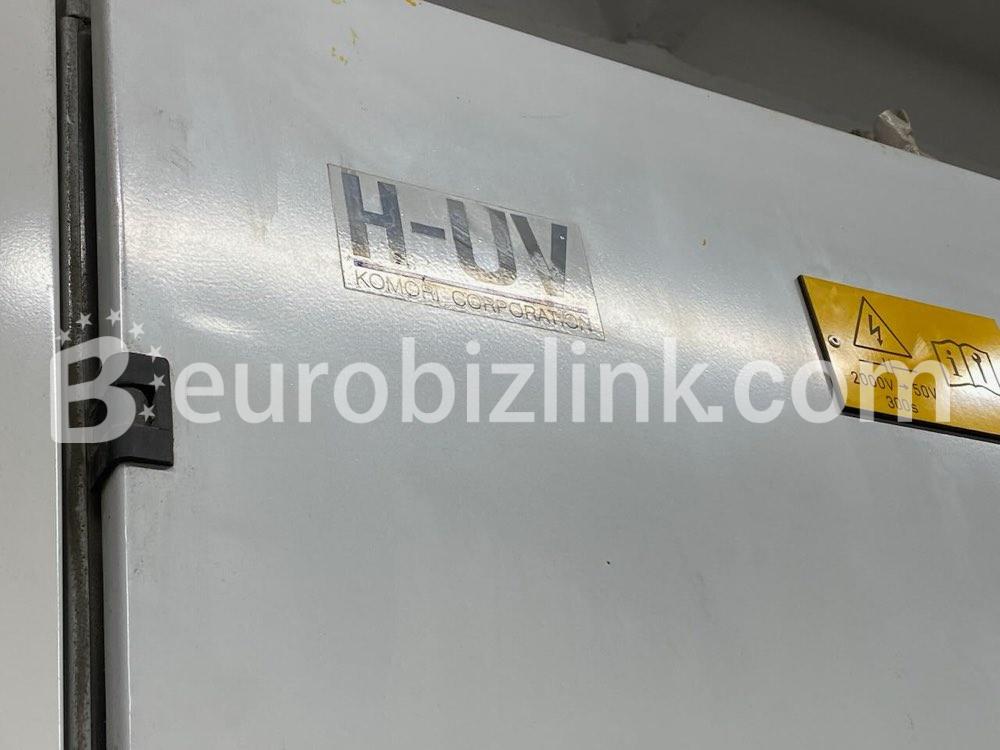
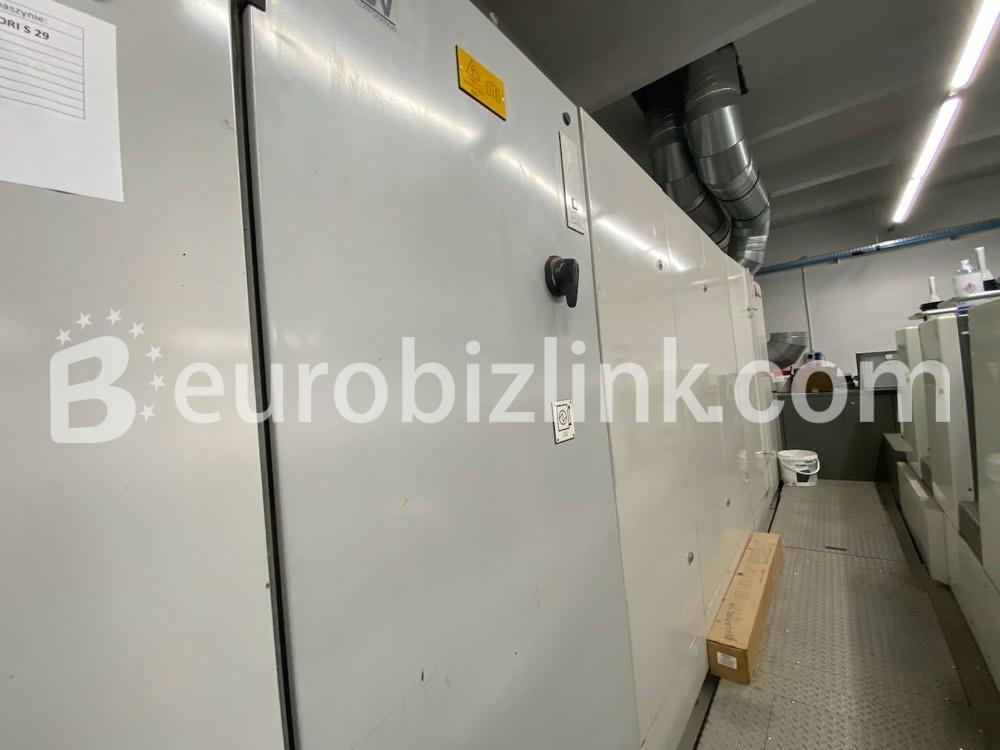
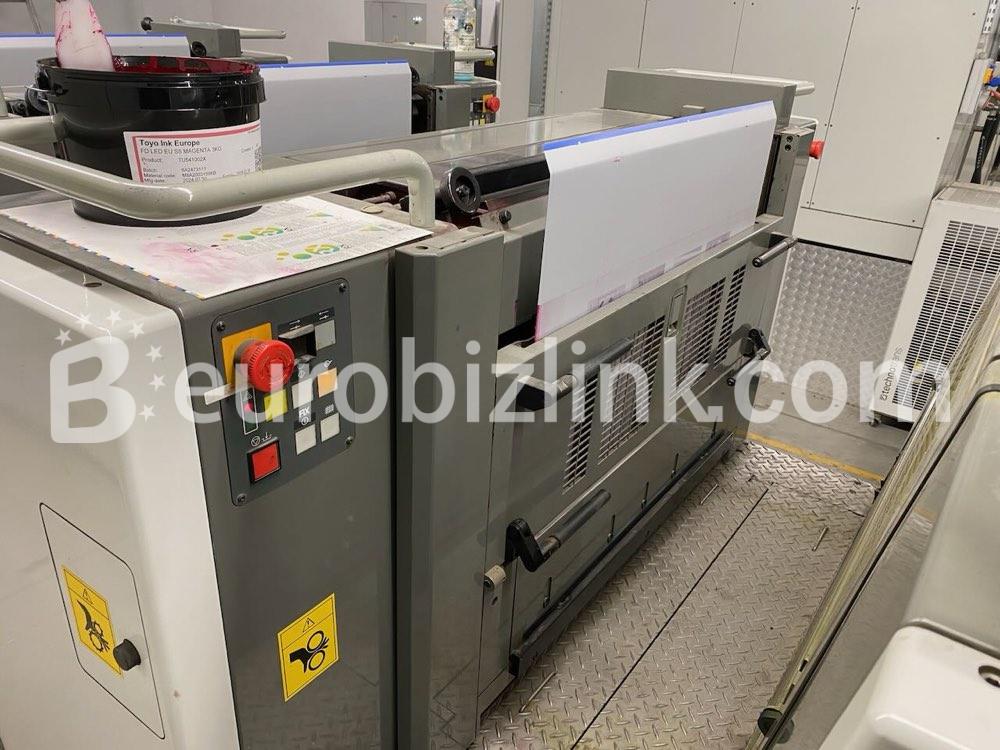
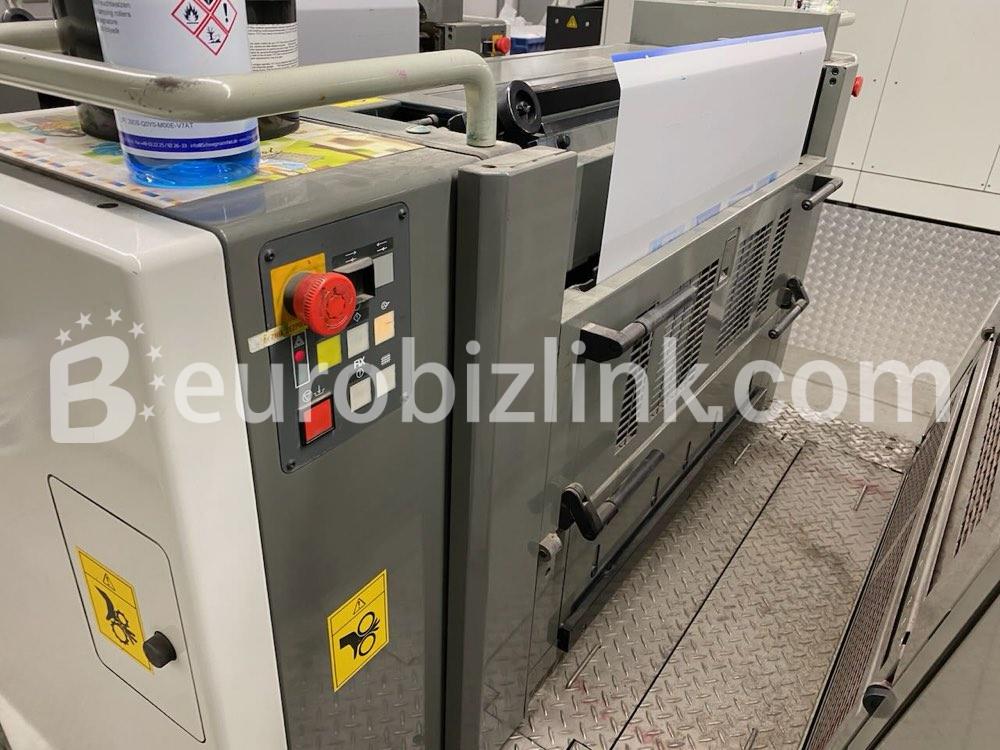
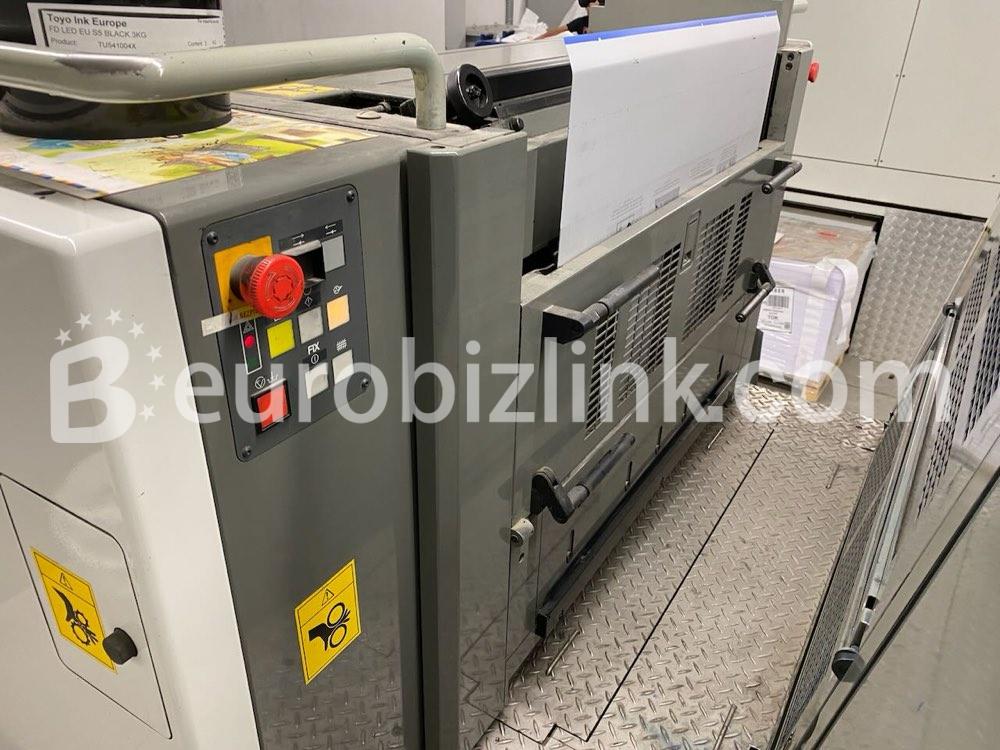

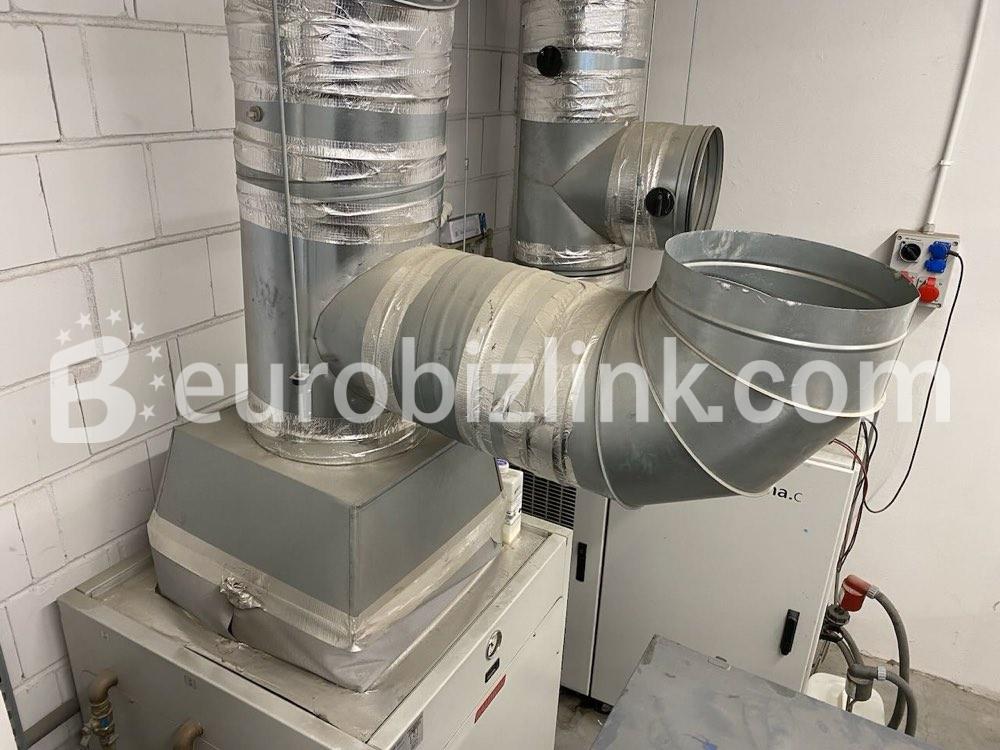
Komori Lithrone LS 429 H-UV
Ref: 100057
Manufacturer: Komori
Year of Manufacturing: 2015
Availability: Immediately
Komori Lithrone LS 429 H-UV
-Year 2015
-4-color offset machine
-Low-energy, ozone-free H-UV system
-Full-APC system – fully automatic plate change
-Max. sheet format 530 x 750 mm
-Max. printing area 520 x 736 mm
-Min. sheet size 257 x 364 mm
-Paper thickness range 0.06 – 0.8 mm
-Plate dimensions 0.3x 605x 745 mm
-Maximum printing speed 16,000 sheets/h
-Minimum printing speed 3,000 sheets/h
-Machine Dimensions: Width 3.13m, Height 1.97 m, Length 7.4 mm
-Weight approx. 17,000 kg
-PQC-S remote quality control system (Print Quality Control-System.
-Remote Dampening control
-Remote control of registers: Longitudinal ( /- 3 mm), Transverse ( /- 1 mm), Diagonally ( /- 0.15 mm) on the transfer cylinder
-KMS 4 machine monitoring system (Komori Management System)
-Komori KHS AI computer-controlled rapid make-ready system, including
-Preset
-High speed start function
-Touch control monitors
-CIP 3.4 DIPS PrintFlow system
-X-Rite EasyTrax D 29” automatic densitometric color control system with PrintFlow software, incorporated in a closed loop in the ink control system.
-Automatic washing of intermediate cylinders
-Automatic washing of pressure cylinders
-Automatic washing of the inking unit (twin nozzle for solvent and water)
-Preset thickness of the printed substrate set from the desktop
-Format preset
-overlay head
-flow table
-Smart sequence function (programming sequences of automatic operations)
-Full-APC system – fully automatic plate change
-Self-jet feeder with a stack height of 1000 mm
-Feeder head equipped with lifting nozzles (2x) and transfer nozzles (2x)
-Deionizing blower in the feeder foot
-Side airflows
-Stack support table adapted for manual stack preparation
-Flow table with one central suction belt
-Sheet stopper on the flow table
-Pneumatic side brand
-Electronic measuring device control
-Electronic control of access to brands
-Diagonal adjustment with a brand strip
-Optoelectronic flow control that disengages the pistons
-Ultrasonic inspection of double sheets (ULTRASONIC)
Printing units
-Double diameter pressure cylinders
-Double diameter transfer cylinders
-Mold cylinder thermally coated with stainless steel
-Standard board thickness 0.30mm backing foil 0.10mm
-Intermediate cylinder thermally coated with stainless steel
-Chrome-plated pressure cylinder
-Intermediate cylinder adapted to attach strip blankets
-Diamond inserts of the transfer paws
-Adjustment of the height of the thresholds on the transfer cylinder
-Setting the cylinders to "seven o'clock"
Inking unit
-Precise regulation of paint feeding (500 steps of opening the ink screw)
-The inking unit is equipped with 19 rollers, including 4 feeding rollers of different diameters
-Tempering of paint grinders
-Anti-wall oscillating rollers transmitting A, B and C on each unit
-Alignment roller on the last feed roller
-Switchable bridge roller connecting the water unit with the dye unit
-Rubber rollers with Weromix technology, for UV and conventional paints
-Separate pick-up drive
-Adjustment of the producer's working time
-Remote control of inking zones from the PQC-S desktop
KOMORIMATIC dampening unit
-Continuous humidification, works perfectly in printing with alcohol and in non-alcoholic printing
-Oscillating leveling roller above the forming roller prevents stenciling and unfavorable stripes
-Reduction of the peripheral speed of the feed roller in relation to the plate cylinder continuously cleans the printing plate for all types of dirt
-Declutching the transmitting shaft drive, allowing you to turn off the delta effect.
-Solution level sensor
-Pneumatic insertion and removal of the transmitting roller from the control panel
Delivery:
-High delivery with a stack height of 1100 mm
-Smoothing sheets (decurler)
-Deionizing beam
-Automatic lubrication of delivery chains